Violent vibration of hydraulic pumps is often a warning of abnormalities in the hydraulic system. This vibration will not only reduce the overall performance of the hydraulic system but may also cause premature wear or even damage to hydraulic components. Accurately identifying and solving the causes of hydraulic pump vibration can effectively improve the operating efficiency and service life of hydraulic equipment.
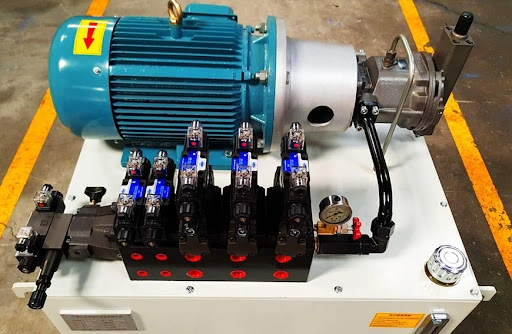
1. Air mixed into hydraulic system
When air is mixed into hydraulic oil, the incompressibility of the hydraulic oil is significantly reduced and cavitation is prone to occur, causing irregular vibrations. This vibration not only affects the working stability of the pump, but also increases the wear of internal components.
Solution:
(1) Check the sealing conditions of fuel tanks, pipelines and other connecting parts to ensure that each joint is tight to prevent air from entering.
(2) Check the hydraulic oil level regularly to avoid air inhalation caused by low oil level.
(3) An air separation device can be used, and if necessary, exhaust by changing oil or using a special exhaust device to ensure that no bubbles remain inside the system.
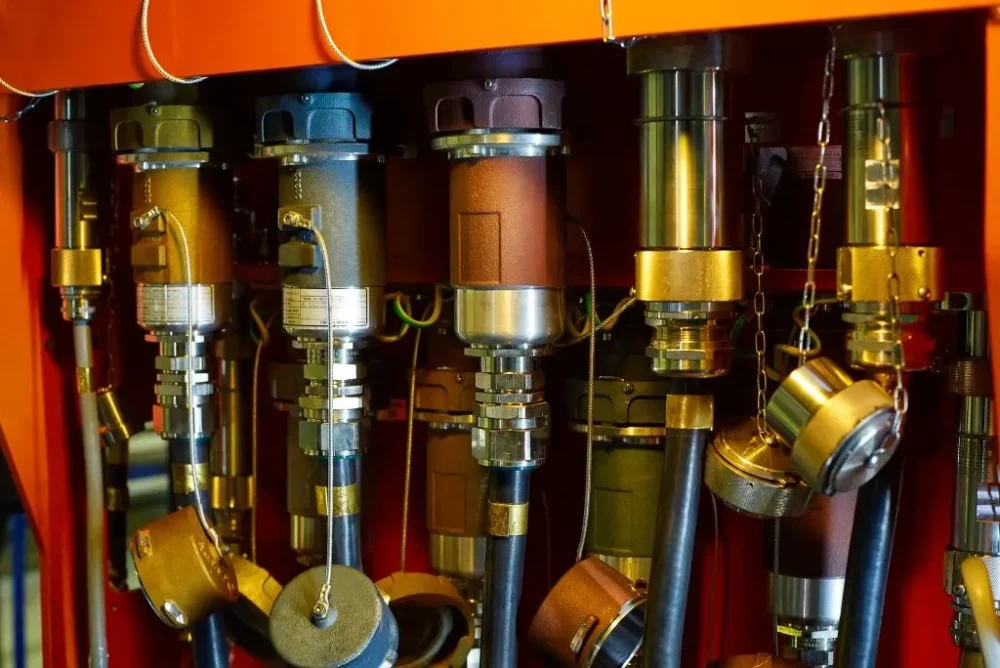
2. The speed of the hydraulic pump is too high
If the speed of the hydraulic pump exceeds the design requirements, the oil suction process will not keep up with the oil discharge speed, resulting in insufficient oil suction and internal pressure fluctuations, causing vibration. This situation is especially prone to occur in high-load and continuous operations.
Solution:
(1)Check the speed of the hydraulic pump and try to keep it within the rated range to avoid exceeding the maximum speed of the pump.
(2)Add or replace a suitable accumulator to stabilize pressure fluctuations and reduce the impact of high speed on the hydraulic pump.
(3)Use an oil suction booster to ensure smooth oil suction at high speed.
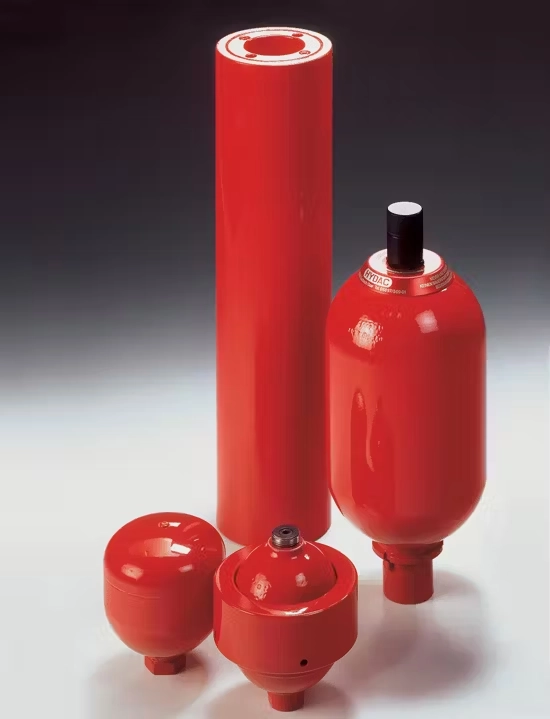
3. Hydraulic system overload
When the load of the hydraulic system exceeds the range it can bear, the load of the hydraulic pump increases, resulting in unstable working state and abnormal vibration. This vibration not only affects the efficiency of the pump, but also shortens the service life of the pump.
Solution:
(1) Evaluate the actual load of the system to ensure that it does not exceed the design load range of the hydraulic pump.
(2) Adjust the load distribution of the system to avoid overloading a certain hydraulic pump.
(3) Install a buffer device or add a diversion device when necessary to reduce the impact of load fluctuations on the hydraulic pump.
4. Inappropriate hydraulic oil viscosity
The viscosity of hydraulic oil directly affects the normal operation of the hydraulic pump. Too high viscosity will increase the oil suction resistance and make the pump difficult to operate; too low viscosity will affect the lubrication performance of the hydraulic oil, increase the friction inside the pump, and cause abnormal vibration.
Solution:
(1) Select suitable hydraulic oil according to the working environment temperature to ensure that the oil viscosity remains within a reasonable range when the temperature difference changes.
(2) Use suitable hydraulic oil and regularly check the oil viscosity to prevent abnormal viscosity.
(3) Replace the hydraulic oil regularly to avoid long-term use, which may cause viscosity drop or impurity accumulation and affect the pump.
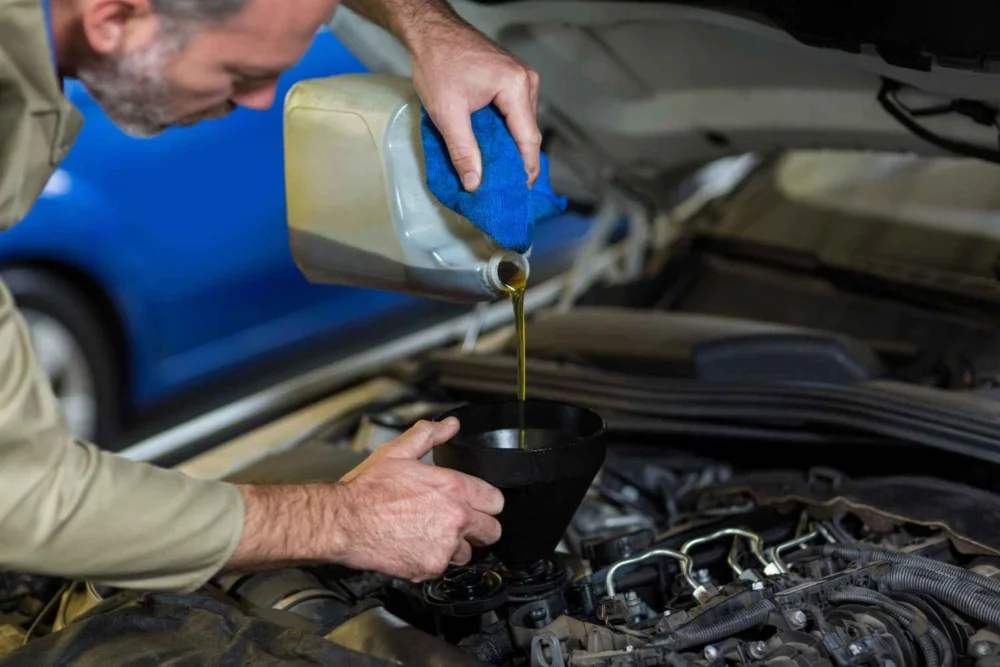
5. Inappropriate hydraulic oil viscosity
The installation quality of the hydraulic pump directly affects its operating stability. If the pump shaft is not aligned with the axis of the drive motor or is poorly aligned, additional mechanical stress will be generated when the pump is working, causing the pump body to vibrate and may even cause other mechanical failures.
Solution:
(1) During the installation process, strictly follow the installation specifications to ensure that the pump shaft and motor axis are aligned to avoid mechanical vibration caused by poor alignment.
(2) Regularly check the stability of the installation location to ensure that the foundation and fasteners are not loose.
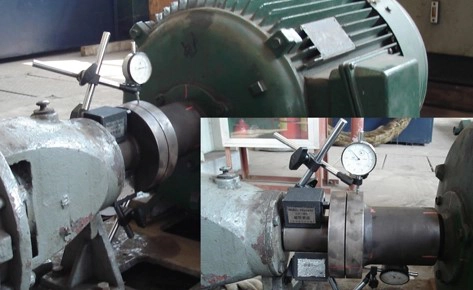