Hydraulic proportional valves and servo valves are more common in hydraulic systems. There is always an ambiguous feeling between the two. So, what are the similarities and differences between them?
1. Similarities
(1) Basic functions
① Hydraulic control:
Hydraulic proportional valves and servo valves are both hydraulic control components. Their core function is to control the pressure, flow and direction in the hydraulic system. By changing the flow state of the hydraulic oil, the actuator (such as a hydraulic cylinder or a hydraulic motor) is driven to complete the corresponding action, such as controlling the extension and retraction of the robot arm and the lifting and lowering of the platform.
② Electro-hydraulic conversion principle:
Both use electro-hydraulic conversion technology. The control of the hydraulic system is achieved by receiving electrical signals. This combination of electrical and hydraulic makes it easy to integrate them into the automation control system and can accurately control the operation of the hydraulic system according to the pre-set program or the operator’s instructions.
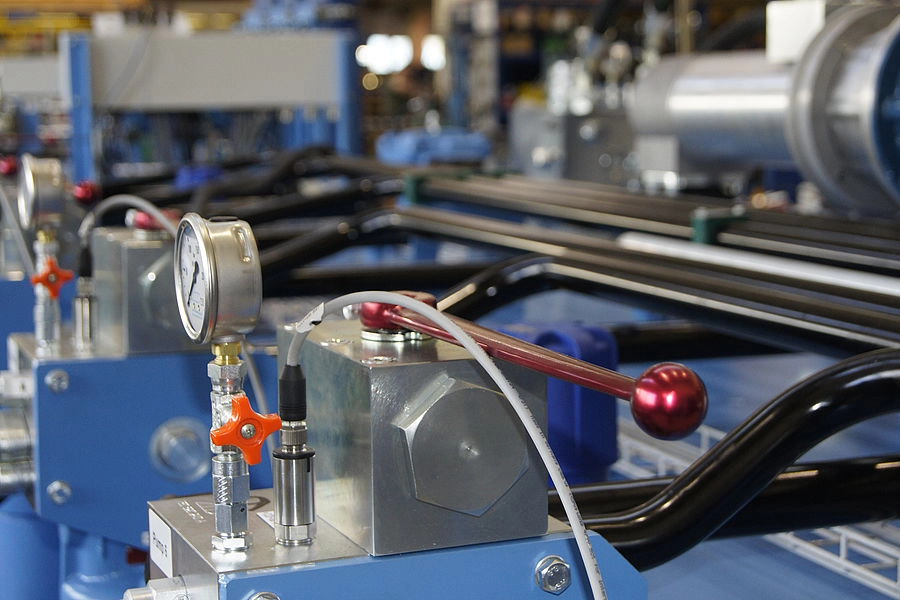
(2) Structural composition
① Both have key components such as valve core:
Structurally, hydraulic proportional valves and servo valves both contain the key part of the valve core. The movement of the valve core is the direct factor in achieving control of the hydraulic oil. Whether it is a proportional valve or a servo valve, the position change of the valve core will change the opening size of the valve port, thereby affecting the flow and pressure of the hydraulic oil. In addition, they are usually equipped with an electromagnetic drive device (such as a proportional solenoid or a torque motor) to convert the electrical signal into the mechanical movement of the valve core.
② The basic structure of the valve body is similar:
The valve body is the basic structure for installing components such as the valve core. The valve bodies of the two valves are similar in appearance and some basic design concepts. They all have basic oil ports such as the oil inlet, oil outlet and oil return port, which are connected through the internal oil channel to ensure that the hydraulic oil can flow in the valve according to the expected path to achieve the corresponding control function.
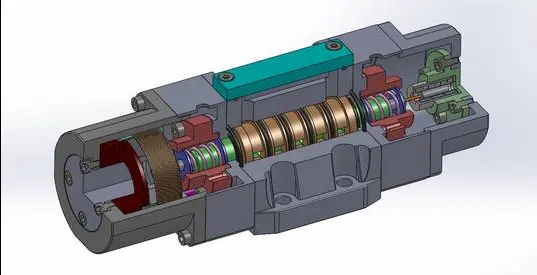
2. Differences
(1) Feedback
① Proportional valves usually use electrical feedback control.
When working, the control signal drives the main valve core to move, and at the same time drives the displacement sensor to generate a feedback signal. When the feedback signal reaches a balance with the given signal, the main valve core stops at the corresponding position to achieve a stable proportional control output.
② Servo valves are mainly divided into two types according to the feedback method:
Mechanical feedback and electrical feedback. The electrical feedback type servo valve uses an electronic sensor for position feedback, which has higher frequency response characteristics and control accuracy; the mechanical feedback type uses a mechanical structure for position feedback. Although the frequency response is low, the structure is simple and reliable, and its dynamic characteristics and working process are basically the same as those of the proportional valve.
(2) Input power
① Proportional valve:
requires a large input power, the working current range is usually 300mA to 1A or more
② Servo valve:
has low power consumption characteristics, the working current is generally only 10-100mA
(3) Control accuracy
① Proportional valve:
relatively low control accuracy, large hysteresis, but relatively loose requirements on oil cleanliness
② Servo valve:
high control accuracy, small hysteresis, but strict requirements on oil cleanliness
(4) Structural distinction
The proportional valve does not have the valve core position closed loop of the servo valve. It is a simplified design form that relies on a large and precise control of the current supplied to the proportional valve core to control the relatively accurate valve core position. The proportional valve does not need to be equipped with a fixed actuator, and the precise realization of position and speed control still requires a system closed loop.
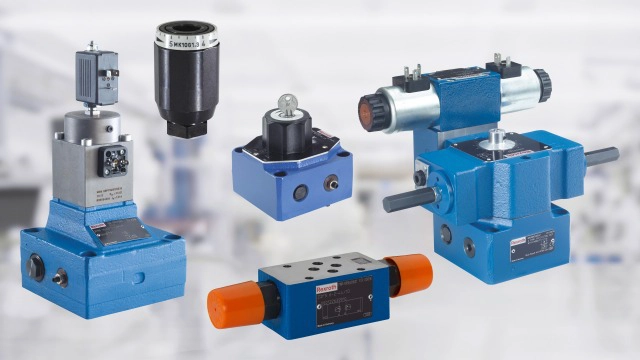
3. Application scenarios:
(1) Hydraulic proportional valve
① Engineering machinery:
In engineering machinery such as cranes, loaders, and bulldozers, proportional valves are used to control the movement of the hydraulic system and realize various complex operations. For example, controlling the lifting and lowering of the crane arm, the digging and unloading of the bucket, etc. Although the control accuracy requirements are not particularly high, reliable performance and moderate cost are required.
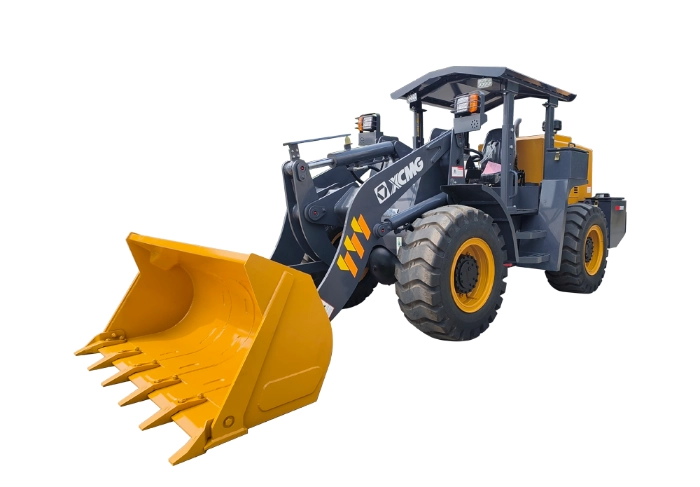
② Injection molding machine industry:
The mold closing, injection, and pressure holding processes of the injection molding machine require precise control of the hydraulic system. The proportional valve can adjust the flow and pressure according to the process requirements to ensure the quality of plastic products. At the same time, due to the harsh production environment of the injection molding machine, the reliability and durability of the proportional valve can also meet the needs.
③ Metallurgical equipment:
In metallurgical equipment such as steel smelting and steel rolling, proportional valves are used to control the hydraulic transmission system to realize various process operations. For example, controlling the pressing device of the rolling mill and the lifting and lowering of the ladle.
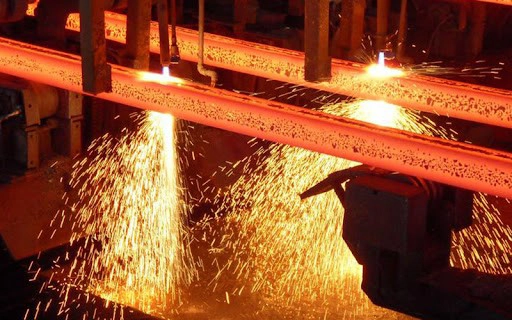
(2) Hydraulic servo valve
① Aerospace:
The flight control system and engine control system of aircraft have extremely high requirements for control accuracy and response speed. The servo valve can accurately control the pressure and flow of the hydraulic system to ensure the safe and stable operation of the aircraft. For example, in the aircraft landing gear retraction and extension system, the servo valve can quickly respond to the control signal to achieve accurate retraction and extension of the landing gear.
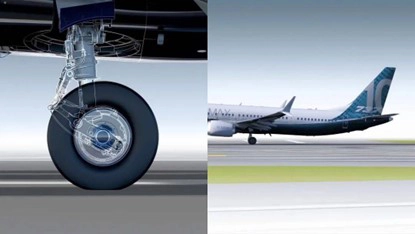
② Precision machine tool industry:
Precision machine tools require high-precision processing and have very high requirements for the control accuracy of the hydraulic system. The servo valve can achieve micron-level displacement control to ensure the processing accuracy and surface quality of the machine tool. For example, in the feed system of the CNC machining center, the servo valve can accurately control the moving speed and position of the workbench.
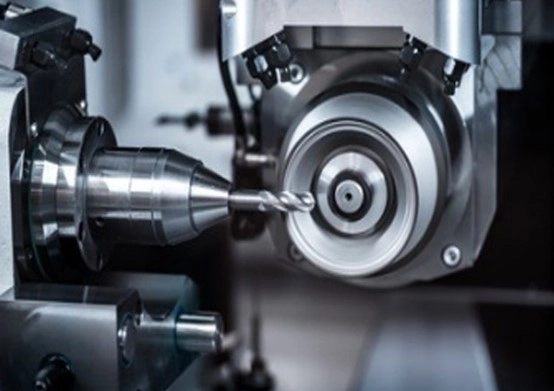
③ Scientific research and experimental field:
In scientific research experiments, the hydraulic system needs to be accurately controlled and measured. The high precision and fast response characteristics of the servo valve make it the first choice. For example, in material mechanics experiments, the servo valve can accurately control the size and direction of the loading force to obtain accurate experimental data.
4. How to choose?
When choosing a hydraulic proportional valve and a servo valve, you need to make a comprehensive consideration based on the specific application scenarios and requirements. If the control accuracy is not high and cost is the main consideration, then the proportional valve is a good choice. If high-precision, fast-response control is required and the cost is not too sensitive, then the servo valve is more suitable.
In short, although the hydraulic proportional valve and the servo valve are somewhat similar in appearance, there are obvious differences in working principles, performance characteristics and application scenarios.
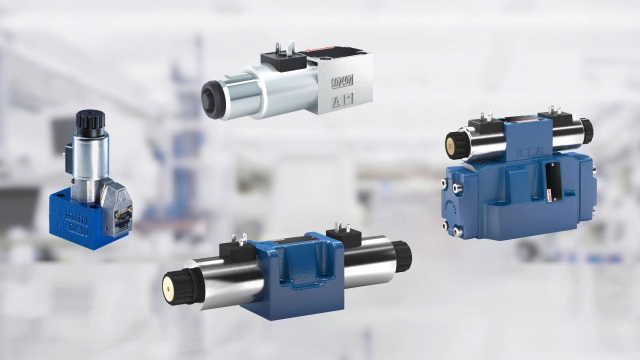